Coho here are BIG, comparable to a Chinook:
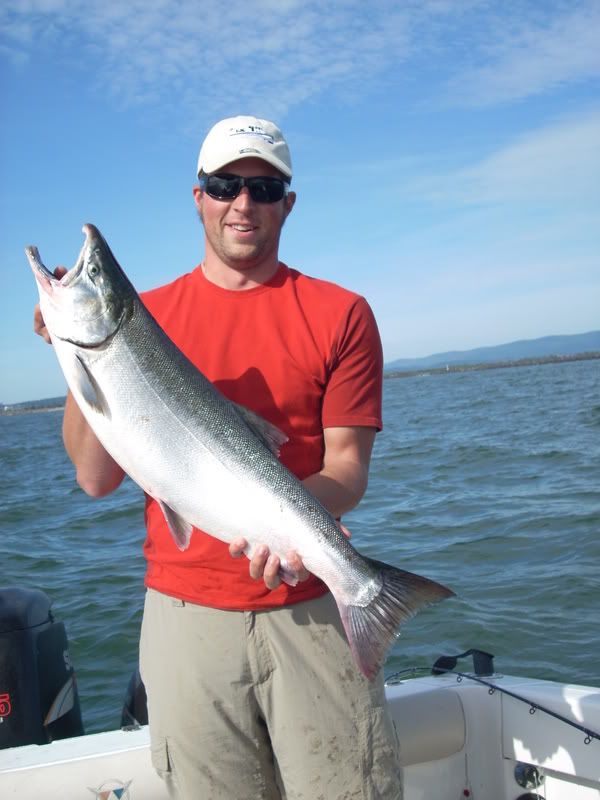
When we returned from picking up 50+ lbs of salmon per guy, it was time to get back to work.
OXFORD
All of the preliminary wood fairing is finished, and epoxy was the excitement today. SWMBO put her best foot forward on this, running the tipping brush (roller cut lengthwise and held with pliers). Roll some on, tip it down.
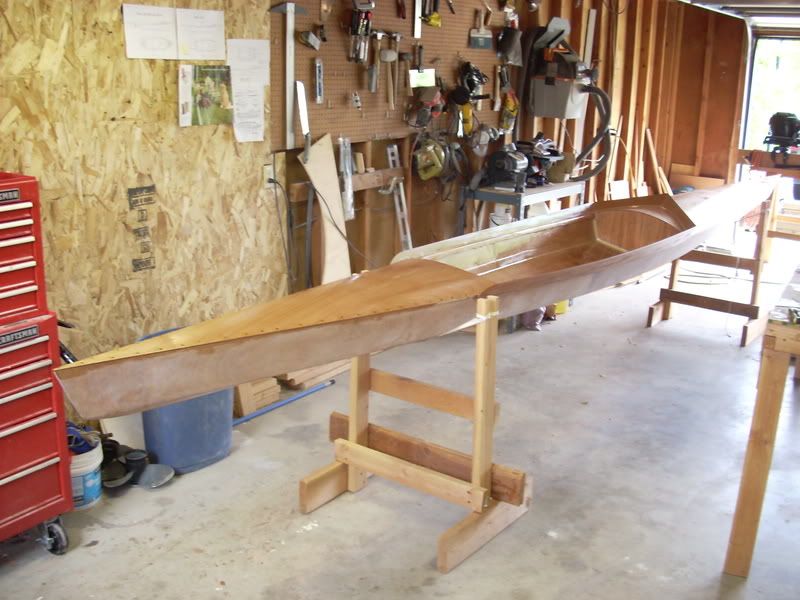
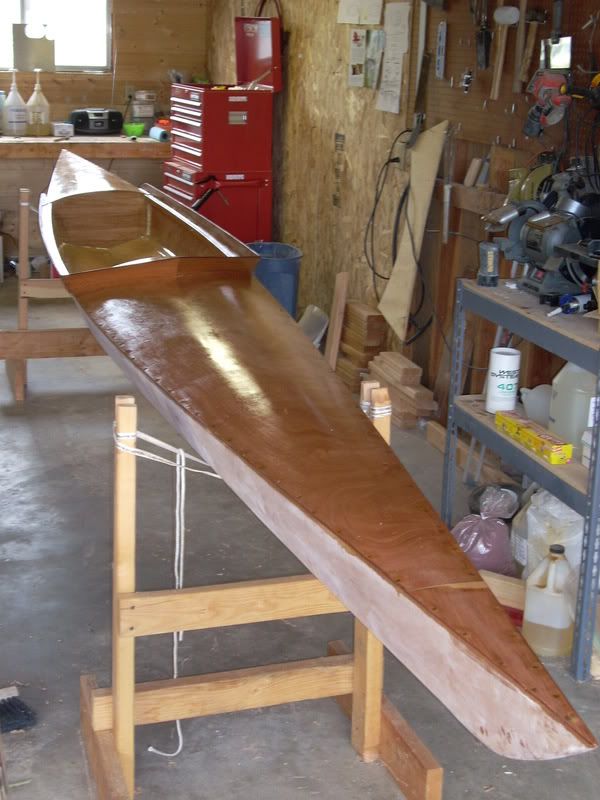
This really brought out the beauty of the structure of the wood, especially around the knots:
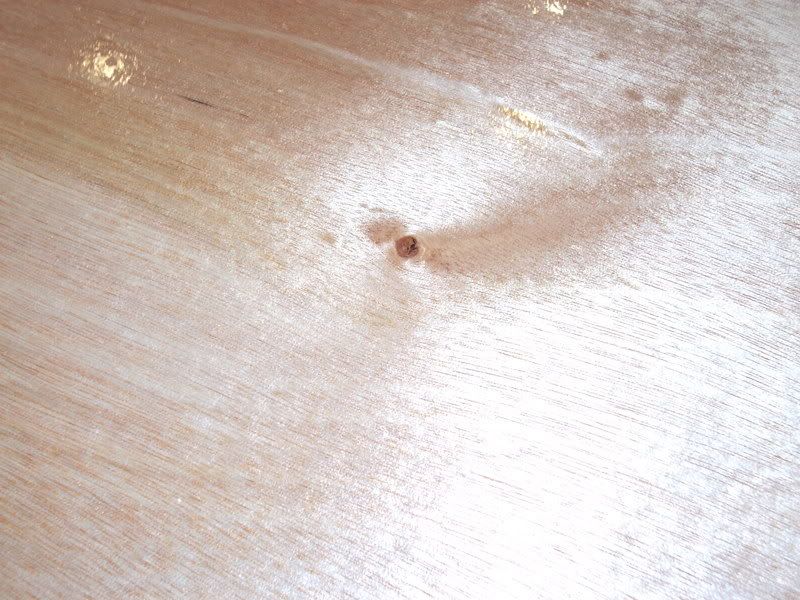
The temps eeked up a little bit after we got the sticky stuff down, which allowed some offgassing. This is where the expansion of gases trapped in the wood slide through the surface and create bubbles in the epoxy. This can be mitigated by doing your epoxy work midday or at the warmest part of the day, or by controlling the temp in your shop. Today it was a balmy 76F, so not like it was epically hot.
Here is a perfect picture of the off gassing bubbles:
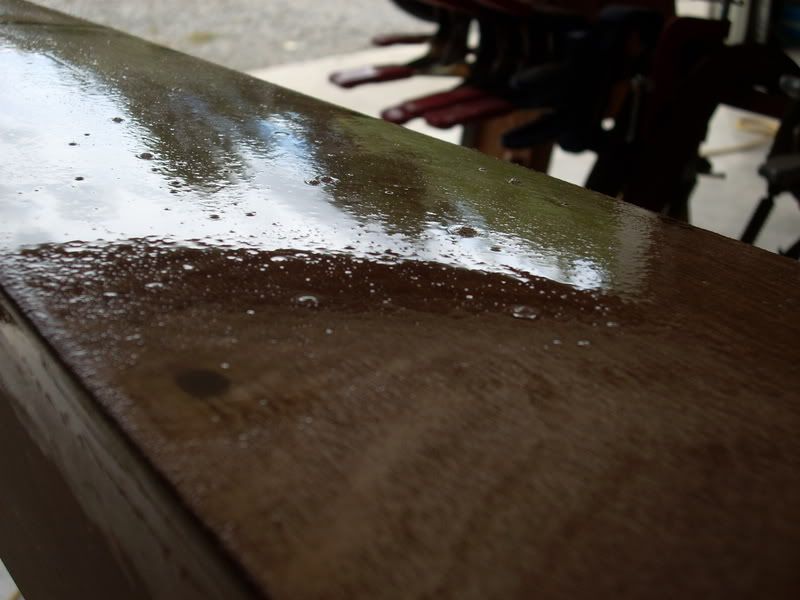
It isn't anything we builder's cant mitigate, however. Just knock the bubble down with a finger, or if it has cured, a scraper, knife, or piece of sand paper. This will cause a small blemish, but since we are early on, there will be fairing occurring later and will be hidden with more layers of epoxy.
Ordered the rigger from www.clcboats.com a few days ago. Great people to work with as they are prompt to respond to questions and have very competitive prices. They are even having their oar supplier do a custom blade and handle for me (Dreher adjustable handles and a set of Apex Hatchet blades). I decided on the RowWing thanks to the help of Chesapeake Rowing and their expertise. Very good experience there as well, and they happen to be the supplier of CLC. Go get your goods from CLC if you can, it works out best for both of the businesses.
This is going to be one helluva sweet setup for SWMBO, I think she will be happy with it.
E